Truing a Spoked Motorcycle Wheel to Spin Properly and Straight
In our lacing a spoked motorcycle wheel article, the technique of how to lace a spoked wheel was explained. All of the spokes have been replaced and the wheel is ready for truing. Truing a motorcycle wheel requires experience and should not usually be done by a novice do-it-yourselfer. If a wheel is out of true, the wheel rim may bend, spokes may bend or come loose and the rider can be seriously hurt. Please consult an experienced mechanic or have it done professionally.
Truing a spoked motorcycle wheel means that it will spin properly and straight. An out-of-true wheel will wobble from side to side or up and down. Quite possibly, it can wobble in both directions. The first step of truing is to find a truing stand. Some people may attempt to do this with the wheel installed in front forks or swing arm of the motorcycle, but this can lead to inaccurate measurements. A truing stand has bearing retainers and height and width adjustment for multiple size wheels.
The spokes should be assembled loosely. The spoke nipples can be tightened to the edge of the spoke thread, just to work as a starting point. Each nipple is slowly turned 1-3 times just to get the spokes tighter. Depending on the number of spokes, the procedure may differ. On a typical 40-spoke wheel, every 4th nipple can be tightened a quarter turn, starting at the valve stem hole. Rotate the wheel as the nipples are tightened with a special spoke wrench. Once around, move down one spoke and tighten every 4th spoke about a quarter of a turn. This is done until every spoke has been tightened. It may take a couple go arounds to get the spokes tight enough to take measurements.
A factory service manual will give wheel offsets. This is measured by taking a straight edge to the bearing flange and measuring the distance from the rim. A guide is used on the wheel stand to give a distance to measure from the rim to the tool. Spinning the wheel will show how close the rim is to spinning true to the guide.
This site and articles contained herein are provided for general informational purposes only and are not a substitute or intended as professional advice. Please be sure to refer to your owner’s manual or consult a mechanic for information specific to your motorcycle. The information contained on this site and articles contained herein are provided on an “as is” basis with no guarantees of completeness, accuracy, usefulness or timeliness and without any warranties of any kind whatsoever, express or implied. Rider Insurance Company, Rider Insurance Agency, Inc. and its affiliates (together, “Rider”) assume no responsibility for any errors or omissions in the content of this site and articles contained herein. Any action taken upon this information is strictly at your own risk and Rider will not be liable for any losses or damages in connection with your use of this site and articles. Additional terms and conditions apply and are available at https://model.rider.com/plymouth-rock-assurance-general-terms-and-conditions/.
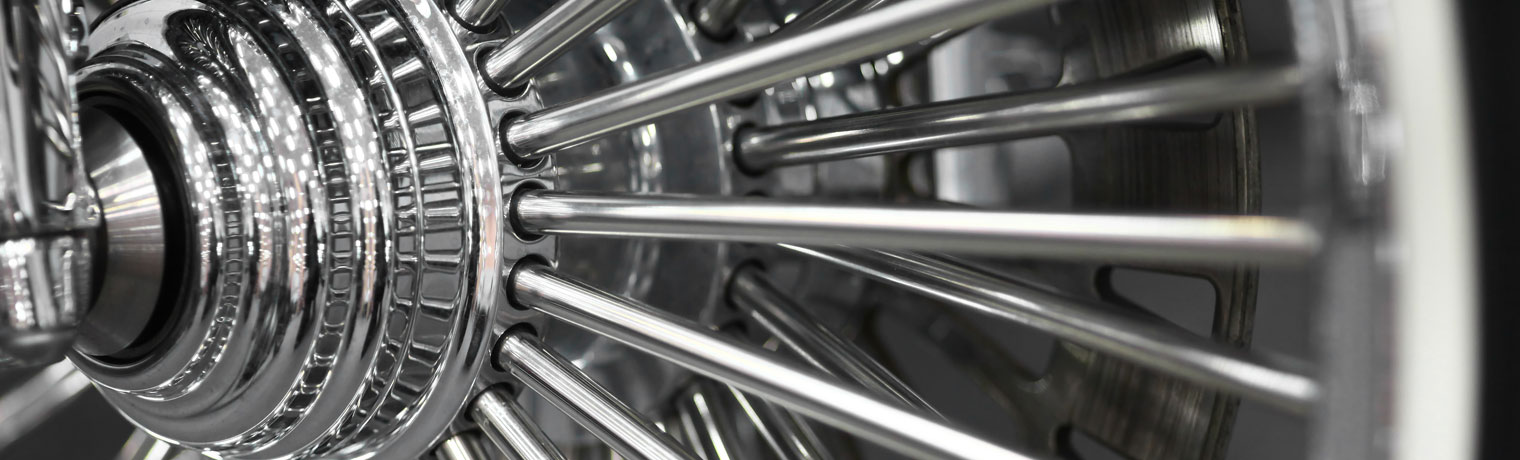
In the same arrangement as the initial tightening, each fourth spoke will be tightened a quarter turn. This will all be carefully measured against the guide. If the wheel comes closer to the guide, the outer spokes may be tightened slightly more to pull it back. If there is a drastic difference, the spokes on the opposite side of the rim will need to be tightened. This will be done until the wheel offset is right. A dial indicator can be placed against the rim to get it trued with the factory specifications. This is not super critical as long as the measurement is close.
The spokes should be pretty tight at this stage. There are special torque wrenches designed to tighten spoke nipples. A lot of modern designed nipples may have an Allen head top. A torque wrench can be applied here to tighten to the factory specifications. Some older wheel builders use a tuning technique where they hit the spokes and listen to the pitch. They tighten all the spokes to the same pitch. Whatever way it is done, the nipples will need to be tightened to the same torque. Once this is all done the wheel should spin tried and true.
Now that the rim is true, the rim strip, tire tube and tire can all be mounted. Any hardware, like sprockets and rotors, can be bolted up and the rim can be balanced. The wheel is then ready to run. Mount the wheel back on the motorcycle and make sure the axles and brake systems are secured and torqued correctly. Take a slow test ride at first to make sure there is no wobble and that everything is working correctly. After some miles, use the spoke wrench/torque wrench and go over the spoke nipples once again. During the riding process a spoke can stretch causing it to come loose. Periodically checking of the nipple torque will ensure smooth operation from the wheel.
Truing a wheel requires experience. Please consult an experienced mechanic or have it done professionally.
Plymouth Rock Assurance is a marketing name used by a group of separate companies that write and manage property and casualty insurance in multiple states. Motorcycle insurance in New Jersey and Pennsylvania is underwritten by Rider Insurance Company. Each company is financially responsible only for its own insurance products. Actual coverage is subject to the language of the policies as issued by each separate company.